case study
Implementing operational excellence in a manufacturing company
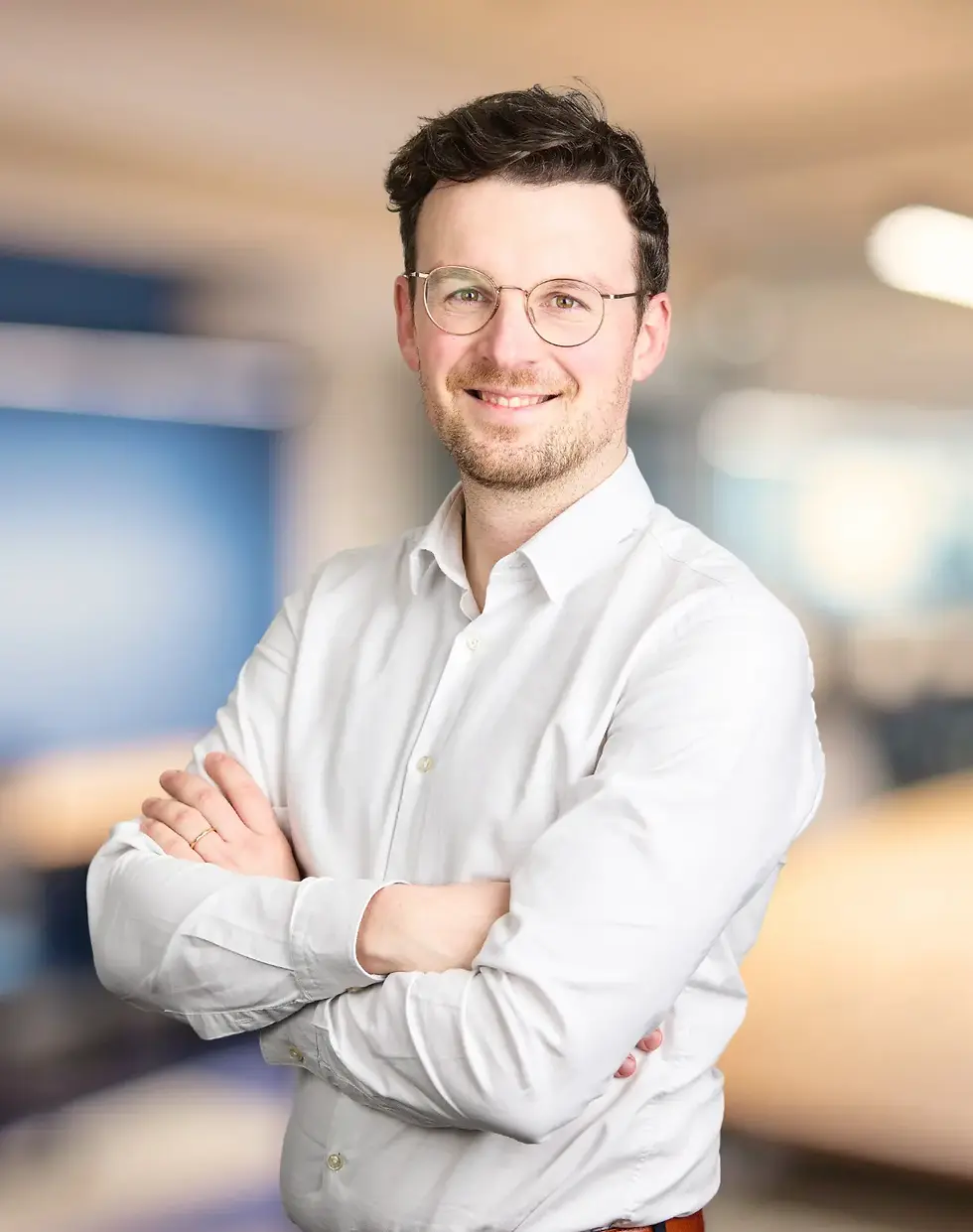
Joris Vanthienen
Running a factory isn’t just about machines: it’s about managing hundreds of variables, people, and processes. A Belgian manufacturer came to BrightWolves after noticing a steady decline in production line performance. With over five lines, dozens of machines, and more than 100 operators, they needed a clear path to regain control. Our mission: embed a culture of Operational Excellence and improve Overall Equipment Effectiveness (OEE) across the board.
.png)
Challenge
To drive performance improvements, the first step was measurement. Without reliable data from their ERP and MES systems, the client lacked visibility into how each production line was performing—or where to focus their efforts. Calculating OEE provided a critical starting point to pinpoint bottlenecks and track progress. However, making changes to long-standing processes—and shifting ingrained mindsets—required more than data. It demanded a deep understanding of operations and a people-first approach to drive change.
Initially, inferior performance was accepted as the norm. By the end of the project, there was a strong drive for continual improvements across the organization.
Approach
We applied a phased methodology tailored to each of the five production lines:
1. Assessment phase
We evaluated current performance and identified key bottlenecks. Weekly OEE figures were calculated by combining data analysis with on-site observations and stakeholder interviews to understand where and why performance was lagging.
2. Pilot phase
Pilot initiatives were launched to address the most pressing issues—ranging from equipment start-up inefficiencies to cleaning routines. Daily progress was tracked, early wins were celebrated, and momentum quickly followed.
3. Roll-out phase
As improvements took hold, we scaled efforts across lines while fostering a culture of continuous improvement. Coaching, job rotations, and process ownership drove engagement. Automated data extraction tools ensured that dips in performance were caught and addressed early.
This scalable approach allowed lessons from one line to be adapted and applied across others—multiplying the impact.

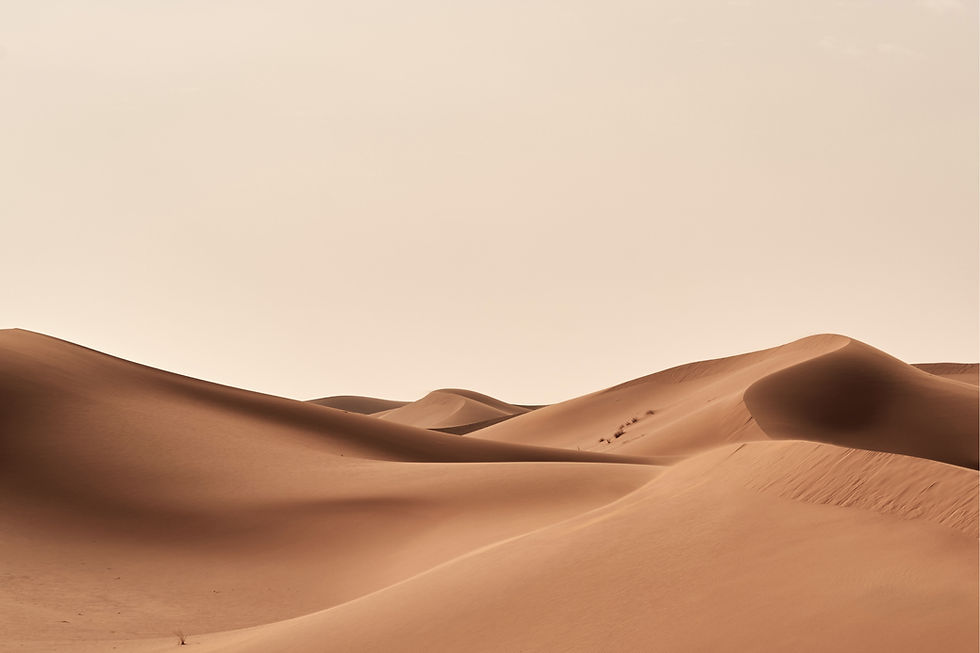
Ready to transform your operations? Operational excellence is within reach. Let’s explore how BrightWolves can help you unlock performance, empower your teams, and build a culture that delivers results—line after line.
Impact
Before the project, OEE wasn’t measured—performance issues were felt but not quantified. With OEE tracking in place, the company identified its biggest inefficiencies and launched over 15 lean initiatives to address them. Improvements in cleaning and start-up procedures alone significantly boosted performance.
Beyond the numbers, a cultural shift was underway. What had been accepted as "just the way things are" was now being challenged. The company developed a strong drive to improve, and performance excellence became the new norm.
Summary
Introduced OEE tracking to create visibility on production performance
Launched 15+ lean initiatives targeting operational bottlenecks
Improved cleaning and start-up routines for measurable OEE gains
Fostered a culture of continuous improvement across all lines
Scaled proven improvements from pilot lines to the full factory